Electronics businesses looking to optimise their process flow and manufacturing capacity should consider adopting a flexible approach to local exhaust ventilation.
Companies have a responsibility to ensure safe working environments for the people they employ – but at the same time, the method they choose to remove potentially harmful airborne contaminants generated during manufacture can be a contributor – or inhibitor – to optimal productivity.
In process-based industries, exposure levels to emissions from, for example, rosin-based solder fume, are tightly mandated through regulated workplace exposure limits. Ineffective extraction will likely lead to the inhalation of fume, causing irritation to the nose, throat and respiratory organs, and placing employees at risk of hypersensitivity, occupational asthma and long-term absenteeism.
Of course, electronics covers much more than soldering, so companies need dust and fume extraction technology capable of mitigating the risks associated, for example, with solvents in conformal coating, with fume associated with PCB marking and printing, adhesives used in dispensing and the fume created by laser depanelling. Each of these presents a health risk for operatives – such as skin and eye irritation, occupational asthma, nausea and dizziness – and BOFA has an effective portable solution for each process.
Which extraction method should you choose?
So how do electronics companies ensure adequate employee protection while simultaneously improving productivity through agile working practices and responsive production line set-up? Making the right choice between a fixed dust and fume extraction infrastructure or a more flexible and configurable portable extraction system can be pivotal in optimising competitiveness.
The checklist for electronics production, engineering and health and safety managers looking at extraction options includes understanding the risk to human health presented by any given process, assessing the installation and life cycle costs of fixed and portable system options, and projecting the future mix of work relative to agility, capability and capacity.
Portable systems, such as those developed by BOFA, provide the extraction performance required by manufacturers along with flexibility to reconfigure workflows quickly without major infrastructure changes. They can also be used to augment an existing vent-to-air (VTA) system.
A centralised VTA system, which extracts contaminants and deposits them outside the building via ducting, might be viewed as a low-cost option (once installed), but life cycle and operating expenditure can be much higher than anticipated, for example, when the cost of replacing heated air extracted from the building is taken into account. Then there’s the negative impact on corporate reputation and on the wider environment of venting contaminants directly into the atmosphere.
Companies also need to be confident that a fixed extraction infrastructure will meet the changing needs of future workflow and processes, otherwise there will be additional costs involved in reconfiguring the ducting and associated extraction hardware.
BOFA Solutions
With BOFA’s multi-stage filtration technology (pre-filters, HEPA filters, and carbon filters), extraction rates of near 100% (99.997%) are achieved, providing both compliant health protection along with the productivity gains that come from fume and dust free process lines. The electronics and laser industries are enthusiastic adopters of this technology precisely because of the effectiveness of the extraction systems and the ability to flex production to meet customer requirements.
Popular BOFA technology for electronics includes the V 250 solder fume extraction system, the V 600 (to remove fine particulates) and the FumeCAB 1000 iQ (to remove fume associated with solvents and chemicals).
In addition, BOFA’s revolutionary iQ operating platform has introduced new levels of control, including independent filter status monitoring to improve extraction efficiency, reduce the risk of downtime and lower the overall cost of system ownership.
To find out more, take a look at our latest electronics case study
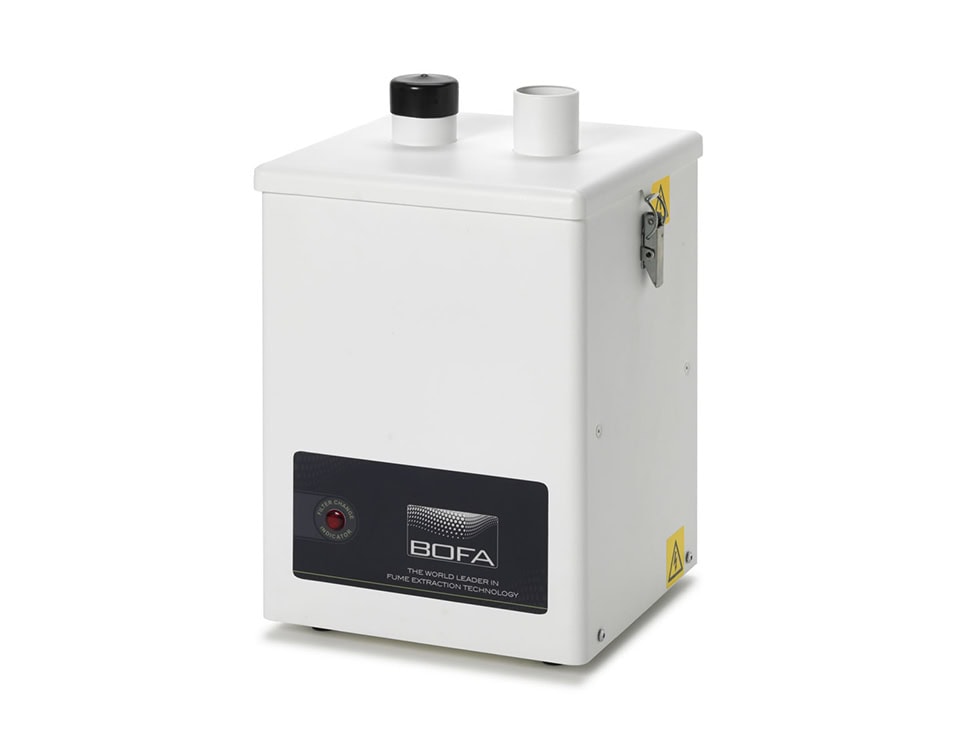
V250 – Front
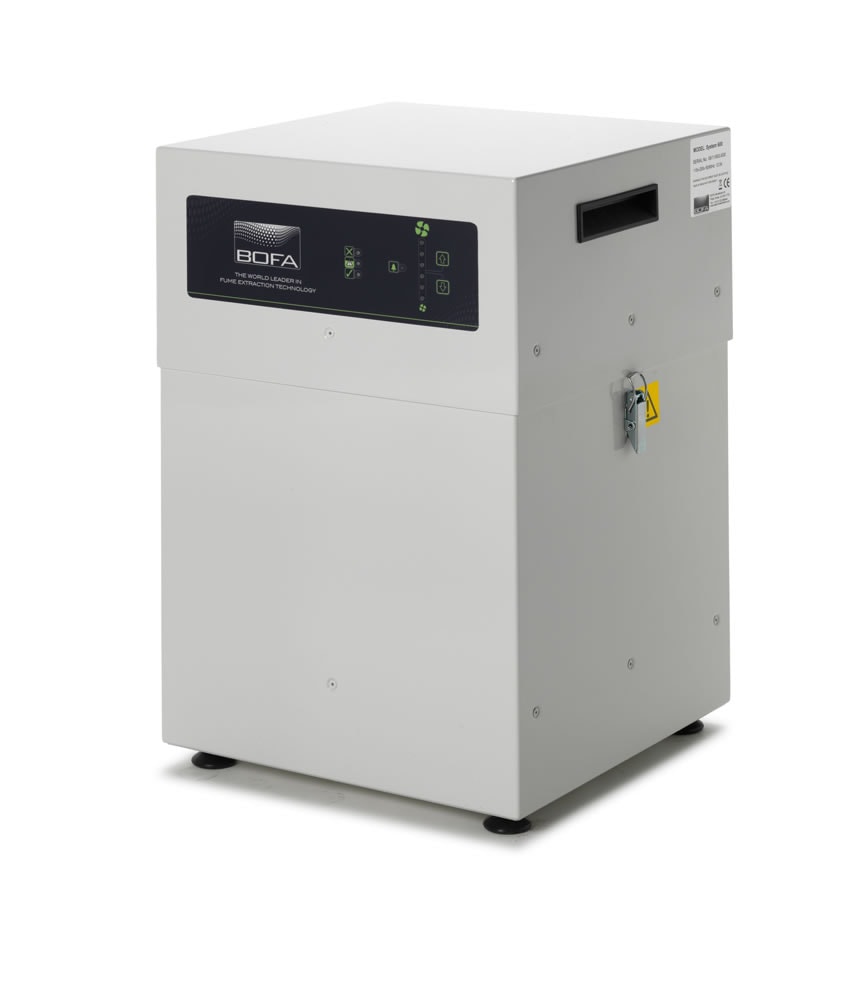
BOFA V 600. Dust & fume extraction system for solder applications and gluing / potting.
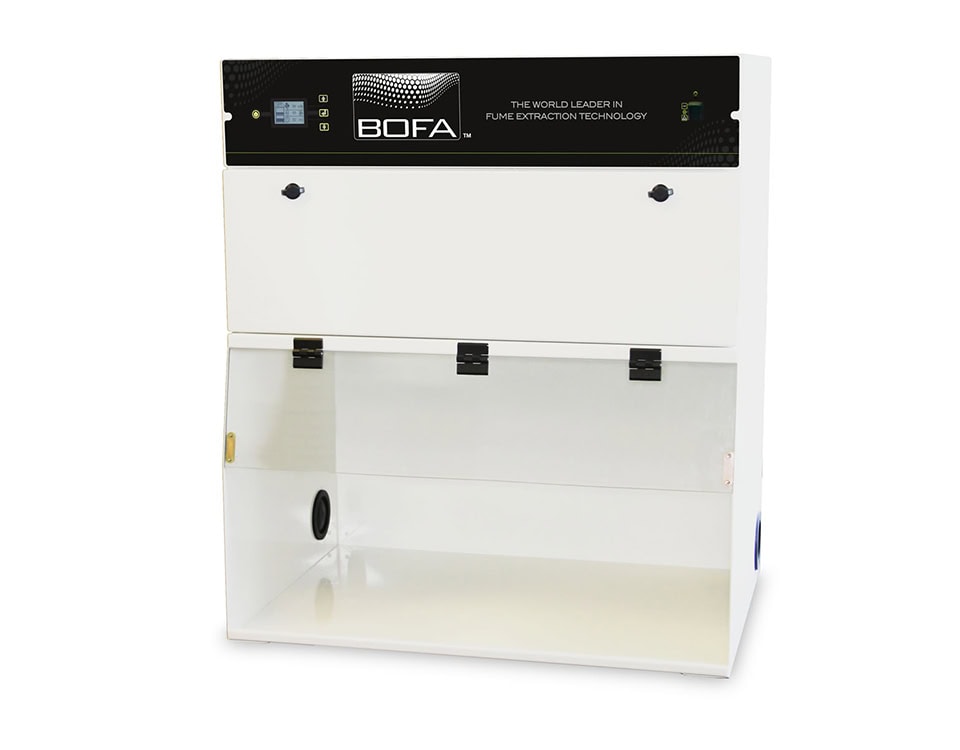
FumeCAB 1000 iQ – Front